- What is a Process Control Chart?
- Variation
- The 4 Process States
- Step-by-Step Guide on Creating a Process Control Chart
- Types and Evolution of Process Control Charts
- Benefits of Process Control Charts
- Historical Context and Evolution of Process Control Charts
- Common Pitfalls and Troubleshooting in Process Control Charts
- Implementation
- Final Thoughts
Donald J. Wheeler, a world-renown expert in continuous improvement, having worked with W. Edwards Deming and later writing the classic book Understanding Variation once said: "Statistical Process Control is, at its heart, about getting the most from your processes. It is about the continual improvement of processes and outcomes. And it is, first and foremost, a way of thinking... with some tools attached."
Well, this article of ours is inspired by his work in a huge way and also, we’d like to thank him for the perfect quote that helps us to put an introduction to process control charts. Why is that so? You’ll understand in a few minutes.
What is a Process Control Chart?
A process control is nothing but a quality control chart that helps monitor and control operation over time. It offers a visual illustration of data, showing modifications and patterns so businesses can make decisions supported by real data. If it’s used in a manufacturing process monitoring system or a service-based industry, control charts are essential for maintaining quality and continuity.
These charts normally include:
- A central line (mean) – Represents the average performance of a process.
- Upper and lower control limits (UCL and LCL) – Indicate acceptable process variation.
- Data points – Actual process measurements plotted over time.
By analyzing these elements, businesses can identify if their operations are under control or if there's a problem that needs solving.
Detailed Explanation of Control Chart Components
To perfectly use a process control chart, you need to understand its main components. Let's understand more about them:
1. Data Points
Every control chart begins with collected data points from the operation tracked. These could be readings of product weight, temperature, or any other important value.
2. Mean Line (Central Line, CL)
This is the average value of the process based on historical data. It acts as the standard for comparison.
3. Control Limits (UCL & LCL)
Control limits are measured based on statistical analysis. They clarify the acceptable range of versions in a process:
- Upper Control Limit (UCL): The highest acceptable value before intervention is needed.
- Lower Control Limit (LCL): The lowest acceptable value before making a move is required.
4. Natural Process Variation vs. Special Causes
- Common cause variation (natural variation): Changes that are expected to stay within the control limits.
- Special cause variation: Strange variations that signal an issue requiring investigation.
Variation
At the point when a process is steady and in charge, as in the above model, you don't see anything yet normal cause variation. Regular cause variation results from the ordinary activity of a process or framework and it is relied upon because of the plan of the process, routine exercises, materials, and different variables.
At the point when a solitary information point falls outside of as far as possible, something startling has happened to the process. Something out of the abnormal has made the process out of control. This is one model of exceptional cause variation. It demonstrates that it's improbable that the information point is because of clamor, haphazardness, or possibility.
Note that process control graphs can uncover issues in any event, when the entirety of the information focuses fall inside as far as possible. In the event that the plot looks non-irregular, with the focuses showing a type of precise conduct, there may at present be something incorrectly.
For instance, in the event that we have eight sequential information focuses above or underneath the normal, that is factually probably not going to be because of possibility. Factual techniques to identify successions or nonrandom examples can be applied to the translation of control graphs. In control measures show arbitrary deviation inside as far as possible.
The 4 Process States
Any process mainly falls into one of four states at any given time:
- Theideal stateoccurs when a process is in statistical control and produces 100 percent conformance to specifications or goals. The process is predictable and produces expected results.
- In thethreshold state, the process is in statistical control but occasionally exhibits non-conformance at times.
- Thebrink of chaosstate refers to a process that is not in statistical control but is not producing defects. This is usually a precursor to the last state;
- The process isout of controland is producing unpredictable non-conformance.
Each process is in one of these states at a particular point in time but doesn’t stay in that state. All processes will move toward the chaos of their own accord, over time, without due attention. Most companies only identify the need for intervention and improvement when the process moves to the out of control state. Control charts help organizations recognize process deterioration so that improvements can be applied to processes in the threshold or brink of chaos state.
Step-by-Step Guide on Creating a Process Control Chart
Applying a process control chart is not as difficult as it sounds. Follow these steps to create one:
Step 1: Define the Process to Monitor
- Spot which process needs improvement, such as product weight in production or response time in customer service.
Step 2: Collect Data Over Time
- Evaluate and record process performance gradually to create a standard.
Step 3: Calculate the Mean and Control Limits
- Using historical data, determine the process mean, standard deviation, and control limits (typically set at ±3 standard deviations).
Step 4: Plot the Data on a Control Chart
- Plot the collected data points, including the mean and control limits.
Step 5: Analyze the Chart for Patterns
- Look for patterns, changes, or sudden signals. A process is unstable if:
- One point is outside the control range.
- A pattern or trend indicates a basic problem.
Step 6: Take Action to Fix
If special cause variation shows up, review and take corrective actions to keep the process maintained and stabled.
Types and Evolution of Process Control Charts
Now that we’ve covered the process control chart’s basics, let’s dive deeper into its types, applications, and historical importance. These insights will help you understand how businesses throughout industries—from manufacturing to IT—leverage control charts to maintain efficiency and quality.
Types of Process Control Charts
Control charts come in various forms, each suited for specific data types and processes. Below are the most common ones:
1. X̄-R (Mean & Range) Chart
- Used when analysing the different versions of a process gradually, particularly when sample sizes are small.
2. X̄-S (Mean & Standard Deviation) Chart
- Similar to X̄-R charts but used when sample sizes are larger, providing a more detailed analysis of process variation.
3. P Chart (Proportion Chart)
- Keeps a record of the percentage of damaged products in a process, normally used in production quality control.
4. C Chart (Count Chart)
- Used for analysing the number of defects in a process per unit. For example, the number of scratches on a car's surface.
5. U Chart (Defects Per Unit Chart)
- Similar to the C chart but changed for varying sample sizes, assuring a fair comparison.
Benefits of Process Control Charts
Organizations that practice continuous quality improvement use control charts to:
- Provide a simple, common language for talking about process performance and behavior
- Make informed decisions about which processes to leave alone and which to subject to an improvement cycle
- Limit the need for inspection
- Determine process capability based on past performance and trends
- Predict future performance if the system is stable and in control
- Assess the impact of process changes
- Visualize the performance of the process over time
- Create a baseline for future improvements
- Communicate the performance of a process
Implementing process control charts for improvements can significantly enhance business performance. Here’s how:
- Improved Decision-Making – Helps businesses use methods supported by real data instead of assumptions.
- Better Process Stability – Guarantees process remains within provided boundaries, minimizing Inconsistency.
- Early problem Identification – Detects problems before they impact production, leading to proactive improvements.
- Improved Quality Control – Plays an important role in production process analysing and maintaining high product standards.
- Regulatory Compliance – Industries following ISO standards, like those obtaining ISO 27001:2022 Lead Auditor Certification, use control charts to ensure compliance.
These benefits make control charts essential for businesses striving for operational excellence.
Historical Context and Evolution of Process Control Charts
The concept of control charts dates back to the 1920s when Dr. Walter A. Shewhart included them as a part of Statistical Process Control at Bell labs. His work creates the foundation for modern quality control charts, impacting industry giants like Toyota and GE.
Over the decades, control charts have evolved to fit in digital transformation. Today, they are a cornerstone of manufacturing process monitoring and service-based process improvements in industries like healthcare, finance, and IT.
To explore more on process documentation further, visit Process Library, a resourceful hub for process standardization.Common Pitfalls and Troubleshooting in Process Control Charts
Even with the best system, control charts can be mishandled. Here are some common mistakes and how to avoid them:
Mistake 1: Confusing Common and Special Cause Variation
- Solution: Only react to special cause variation, not normal fluctuations within control limits.
Mistake 2: Setting Arbitrary Control Limits
- Solution: Use statistical analysis to evaluate boundaries rather than choosing them randomly.
Mistake 3: Ignoring Process Trends
- Solution: Watch for patterns, such as repeated upward or downward trends, even if points remain within limits.
Mistake 4: Depending on Control Charts Without Further Analysis
- Solution: Combine charts with process control charts' analysis to apply corrective actions effectively.
Implementation
There are a few basic steps to implementing a control chart.
Step 1: Define what needs to be controlled or monitored
Step 2: Determine the measurement system that will supply the data
Step 3: Establish the control limits based on some baseline data
Step 4: Collect and chart the data
Step 5: Make decisions based on the correct interpretations control chart information
Process Control Charts are mainstream with assembling associations utilizing the Lean or Six Sigma business system, however, they can be of extraordinary worth when applied to any cycle that has quantifiable results that can be followed after some time. Organizations of different types can profit by this basic, yet ground-breaking approach to picture process performances.
To be continued for Why Process Control Charts are a Roadmap to Improvement
Final Thoughts
A process control chart isn't just a graph—it's a powerful tools for confirming process stability and pushing continuous improvement forward. Whether in manufacturing, IT, or service industries, control charts help organizations reduce defects, maintain consistency, and enhance operational efficiency.
To master process monitoring techniques and elevate your quality management skills, explore more with NovelVista and get certified in industry-leading standards.
Ready to Take Control of Your Processes?
👉 Read our beginner-friendly guide to Process Control Charts now!
Author Details
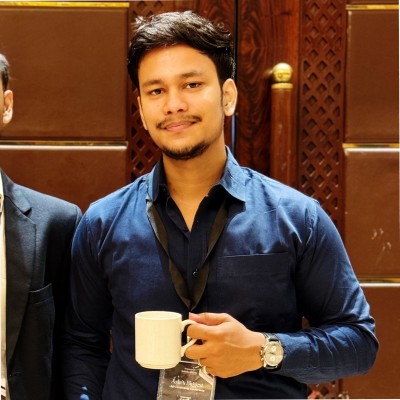
Vaibhav Umarvaishya
Cloud Engineer | Solution Architect
As a Cloud Engineer and AWS Solutions Architect Associate at NovelVista, I specialized in designing and deploying scalable and fault-tolerant systems on AWS. My responsibilities included selecting suitable AWS services based on specific requirements, managing AWS costs, and implementing best practices for security. I also played a pivotal role in migrating complex applications to AWS and advising on architectural decisions to optimize cloud deployments.
Confused About Certification?
Get Free Consultation Call