- First, what are TQM and QMS?
- What is Total Quality Management (TQM)?
- What is a Quality Management System (QMS)?
- Understanding Total Quality Control (TQC)
- TQM vs QMS: Breaking Down the Differences
- What is the difference between TQM and QMS?
- Quality Assurance vs Quality Control
- QMS Audit vs TQM Assessment: Measuring Quality
- How to develop QMS vs TQM?
- Implementing TQM and QMS: Best Practices
- Benefits of TQM and QMS
- Final words: Which One Should You Choose?
- Conclusion:
In the modern landscape of industries, businesses are looking for different methods by which they can continuously enhance their products and services. Total quality management vs quality management-these are the two concepts that have gained significant prominence in the pursuit of excellence. But how do these two concepts compare, and how do they conflict with each other?
In this blog, we will explore the fundamental differences between quality management vs total quality management. Also, we will highlight the unique characteristics, features, and applications.
First, what are TQM and QMS?
Total Quality Management (TQM)
Total quality management is the management approach for long-term success, which is done through consumer satisfaction. This initially came out of manufacturing, but its acceptance saw it move into nearly all sectors. TQM concentrated on enhancing the processing to improve consumer satisfaction, often following the cycle of Plan, Do, Check and Act known as (PDCA).
It integrates quality principles throughout the entire business, from top-level management to front-line employees. It contributes to the culture of teamwork, collaboration, and accountability where all professionals or individuals are responsible for delivering high-quality services and products. With the help of embracing TQM, businesses aim to optimize efficiency, decrease waste, improve consumer experiences, etc.
Most of the time, it is managed by individuals rather than developed across entire businesses. Following are the different principles of TQM and one thing you need to understand is they are similar to Total Quality Control but with a few differences.
- Concentration on consumers
- Involve people
- Adopt a process-driven approach
- Integrate organizational systems
- Adopt a strategic and systematic methodology
- Adopt the factual method of decision-making
- Make sure communication with stakeholders goes well
- Commit to continual enhancement
Features of Total Quality Management
- Target:It’s the essential factor of TQM as it achieves quality. The quality policy must be set toward consumers. Meeting consumers' requirements means sustaining every consumer's needs, but not reaching the quality standards set beforehand.
- Scope:With the extension of the production procedure to suppliers and sub-contractors, quality products and services can be achieved in TQM. The approach of placing an order must be suitable, too, but only if the candidate does quality assurance.
- Form:Another significant factor of TQM is it controls the quality of the input even before the production procedure starts. It doesn’t deal with the finished products at all. There are set-up plans and programs right before the development starts.
- Basis of the TQM system:We know that humans are the basis of TQM, but when we talk about quality, people usually think about the quality of the products. But, in this, it’s the quality of the resource persons that prominences are placed on.
Quality Management System (QMS)
A Quality Management System is known as a set of business procedures that are geared towards offering the products and services to consistently high standard. The effective QMS will align with the plan for continuous measurement and enhancement along with the quality commitment.
It is mostly adopted across the entire business, bringing operations in line with the same requirement and standards to provide consistency and quality at all levels. Once they have developed the QMS is up to standards and issues them with the notification such asISO. Following are the key principles of Quality Management System.
- Concentration on consumers
- Offering strong leadership
- Involve people
- Adopt the procedures
- Adopt the systematic approach to management
- Commit to continual enhancement
- Understand the supplier relations are mutually beneficial
What is Total Quality Management (TQM)?
TQM is all about merging quality into your organization’s culture. It’s an approach that focuses on continuous improvement, making every employee—from top leadership to front-line staff—responsible for quality across all industries.
Think of it this way: TQM is not only about checking if a product meets quality standards; however it is about assuring quality is built into every step of the process.
Core Principles of TQM:
- Customer Focus: Everything starts with knowing the customer's needs.
- Employee Involvement: Everyone positions themselves in maintaining and improving quality.
- Process Optimization: Identify weaknesses and improve them continuously.
- Continuous Upgrades (Kaizen): Small, regular improvements lead to long-term success.
- Data-Driven Decisions: Use measurements and analysis to trace progress and identify problems.
TQM is widely used in industries like manufacturing, healthcare, finance, and IT to improve efficiency, minimize waste, and boost customer satisfaction.
What is a Quality Management System (QMS)?
Unlike TQM, which is about change, QMS is a structured system of policies, processes, and procedures designed to guarantee consistent quality and legal compliance. QMS is often aligned with international standards like ISO Quality Standards and ISO 27001, making it a preferred choice for businesses that need formalized quality frameworks.
Key Features of QMS:
- Structured Operations: Helps maintain stability across departments.
- Legal Compliance: Meets sector-relevant quality and data protection requirements.
- Risk Management: Identifies and Minimizes possible risks.
- Documented Guidelines: Provides clear guidelines on quality control.
- Flexibility: Works for companies of all sizes, from startups to enterprises.
For companies that require to demonstrate compliance and assure operational efficiency, QMS provides a structured and regulated approach to quality.
Understanding Total Quality Control (TQC)
Total Quality Control is the organized Kaizen activities which includes everyone in the business managers and workers in totally incorporated effort toward enhancing performance at every level.
Total Quality Control is the narrower factor which primarily concentrates on the inspection and control of product quality. It emphasizes statistical quality control techniques to detect and reduce defects at the time of production processes. This approach includes the series of quality checks and inspections to make sure that final products meet the specified quality standards.
TQC includes setting up quality control systems developing statistical procedure control system and methods. It involves conducting rigorous testing to identify and address any deviations from the desired quality levels.
Also by thoroughly monitoring production procedures and retaining quality control tools, businesses using TQC aims to lessen defects and enhance the product reliability and increase consumer satisfaction.
Download: TQM vs QMS Case Study Bundle
Learn how top companies turned quality
challenges into lasting success.
TQM vs QMS: Breaking Down the Differences
While both TQM as well as QMS aim for quality excellence, they differ in approach, focus, and implementation.
Criteria |
TQM |
QMS |
Approach |
Cultural and holistic |
Structured and process-driven |
Focus |
Continuous improvement, customer satisfaction |
Compliance and regulatory adherence |
Implementation |
Employee-driven, company-wide |
Process-driven, documentation-focused |
Flexibility |
Adaptable to any business |
Best for regulated industries |
Assessment |
TQM evaluation (cultural adoption) |
QMS audit (standards compliance) |
Industry Use |
Ideal for customer-focused firms |
Important for ISO-certified businesses |
So, if you're looking to encourage a culture of continuous improvement, TQM is the best choice. But, if you require compliance and paperwork for industry standards, QMS is the better choice.
What is the difference between TQM and QMS?
TheTQM vs QMSsystems are both comes under the management philosophies which concentrated on enhancing the overall quality of products and services. Although, there are different key factors among these two approaches.
First, TQM comes with holistic approach. It is quality management that concentrates on enhancing all aspects of the business. From its products and services to the overall procedures and cultures. It’s based on the belief that everyone in a business has the role play in enhancing quality and it should be everyone’s responsibility.
Second, QMS has the more structured approach to quality management which focuses on the systematic development of quality management practices. It’s mostly depend on the use of the set of standards like ISO 9001 which defines the requirements for the quality management system. QMS is communally used by businesses to demonstrate their commitment to quality to consumers, suppliers and other stakeholders.
Following is clear and in-depth demonstration of differences of QMS vs TQM:
Parameters |
TQM |
QMS |
Aim |
It seeks to holds all manufacturing procedure engagement initiatives accountable for the products as well as service which is delivered in the end. |
It has aim of constantly satisfy client requirements. |
Leadership |
TQM in contrast doesn’t provide effective leadership. |
QMS has very strong leadership. |
Relations |
The mutual advantages of supplier relationships aren’t given great weight in TQM. |
Supplier relationships which are beneficial to both parties are acknowledged by QMS. |
Scope |
All aspects of the business |
Quality management practices |
Responsibility |
Everyone in the business |
Management only |
Application |
TQM is applicable for all functional areas and levels of the business. It includes the integration of quality principles into each aspect of business such as from strategic planning to daily operations. |
It is predominantly employed within manufacturing or production based environments where quality control and defect prevention are critical. |
Now, which approach is best?
The best approach in quality management for your business will depend on the specific requirements and gaols. If you are looking for holistic approach which includes everyone in business and support all aspects of your business then TQM might be a great choice for you.
If you are looking for the more structured method or approach which will help you to comply with the standards and demonstrates your commitment to quality to consumers and stakeholders then QMS might be a better choice.
Quality Assurance vs Quality Control
Let’s clear up a common confusion:
- Quality Assurance (QA): Active approach guaranteeing that processes avoid defects (aligned with QMS).
- Quality Control (QC): Reactive approach that identifies and solves defects (aligned with TQM).
While QMS focuses on preventive measures and compliance, TQM emphasizes ongoing quality enhancement at every level.
QMS Audit vs TQM Assessment: Measuring Quality
QMS Audit: A structured analysis ensuring that a business meets industry rules. This is important in industries like healthcare, IT, and manufacturing that require Information Security Management and compliance with ISO Auditing Practices.
TQM Assessment: Measures cultural adoption and quality improvements within an organization.
If an organization needs to obtain ISO certification, a QMS audit is mandatory. However, for internal improvements and innovation, a TQM assessment is more effective.
How to develop QMS vs TQM?
If you decide to developTQM vs QMSthere are a few key factors you need to look for:
- Get executive Buy-In:TQM and QMS aren’t initiatives which can be developed by the single department or group. They require the support and obligation of upper management.
- Generate the Plan:Once you have executive buy-in, you require to generate the new plan for how you will development ofQMS vs TQM. It needs to be consider your goals, objectives and the timeline for development.
- Train your employees:It’s essential to train your employees on the principles of TQM and QMS. Its training will help employees to understand their roles and responsibilities in enhancing quality.
- Measure your progress:It’s essential to measure your progress as you develop TQM or QMS. It will help to track your progress and make improvements as needed.
- Get Feedback:It’s also essential to get feedback from your employees, consumers, and other stockholder’s. This feedback will allow you to enhance yourtotal quality management vs quality management
Implementing TQM and QMS: Best Practices
Thinking about how to start the journey? Here are some actionable plans for executing TQM as well as QMS effectively.
TQM Implementation Strategies:
- Develop a quality-first mindset: Train employees on constant upgradationss.
- Encourage employee contribution: Quality should be everyone's responsibility.
- Use customer feedback: Focus on improving customer satisfaction.
- Track progress: Use measurements and KPIs to measure quality improvements.
QMS Best Practices:
- Meet ISO standards: Align with ISO 27001 Certification Course Training for structured compliance.
- Document all procedures: Assure all quality policies are clearly stated.
- Conduct regular audits: Use QMS audits to trace compliance and identify gaps.
- Merge with risk management: Resolve possible process failures actively.
By following these best practices, businesses can maximize the benefits of TQM and QMS while ensuring efficiency and compliance.
Benefits of TQM and QMS
Both TQM along QMS come with unique benefits, depending on the organisation’s goals and needs.
Top Benefits of TQM:
- Promotes innovation and efficiency by involving all employees.
- Improves customer satisfaction by delivering high-quality products.
- Minimize waste and operational inefficiencies through continuous improvement.
- Boosts teamwork and collaboration within the organization.
Top Benefits of QMS:
- Ensures regulatory compliance with standards like ISO 9001 & ISO 27001 Objectives.
- Regulates operations to maintain consistency and quality.
- Improves risk management by identifying possible process failures.
- Boosts credibility in highly regulated industries like finance, healthcare, and IT.
Many organizations combine TQM plus QMS to get the best of both worlds—a culture of continuous improvement backed by structured quality management systems.
Final words: Which One Should You Choose?
The choice between TQM or QMS depends on your company's priorities:
- Want to create a company-wide culture of constant upgradation? → Go with TQM.
- Need to meet industry regulations and formal compliance? → Implement QMS.
- Looking for the best of both worlds? → Combine TQM principles and QMS standards for maximum efficiency.
Regardless of the path you choose, a strong focus on quality will always lead to business success.
Want to know how both TQM and QMS meet ISO standards? Have a look at the ISO 27001 Certification Course Trainingat NovelVista!
TQM vs QMS: Know the Key Differences!
Enhance Your Quality Management Knowledge.
Conclusion:
The above blog has elaborated on the in-depth specifications and differences of TQM and TQC. While TQM and TQC share the communal objective of achieving high quality standards, they also differentiate their scope, focus, applications and approach. Total Quality Management successfully emphasizes the overall business development, enhancement, consumer satisfaction, and continuous improvement, including all individuals within the business.
Regarding Total quality control focuses on quality control during production processes, employing inspections, statistical techniques, and testing to make sure the final product meets the desired standards.
Author Details
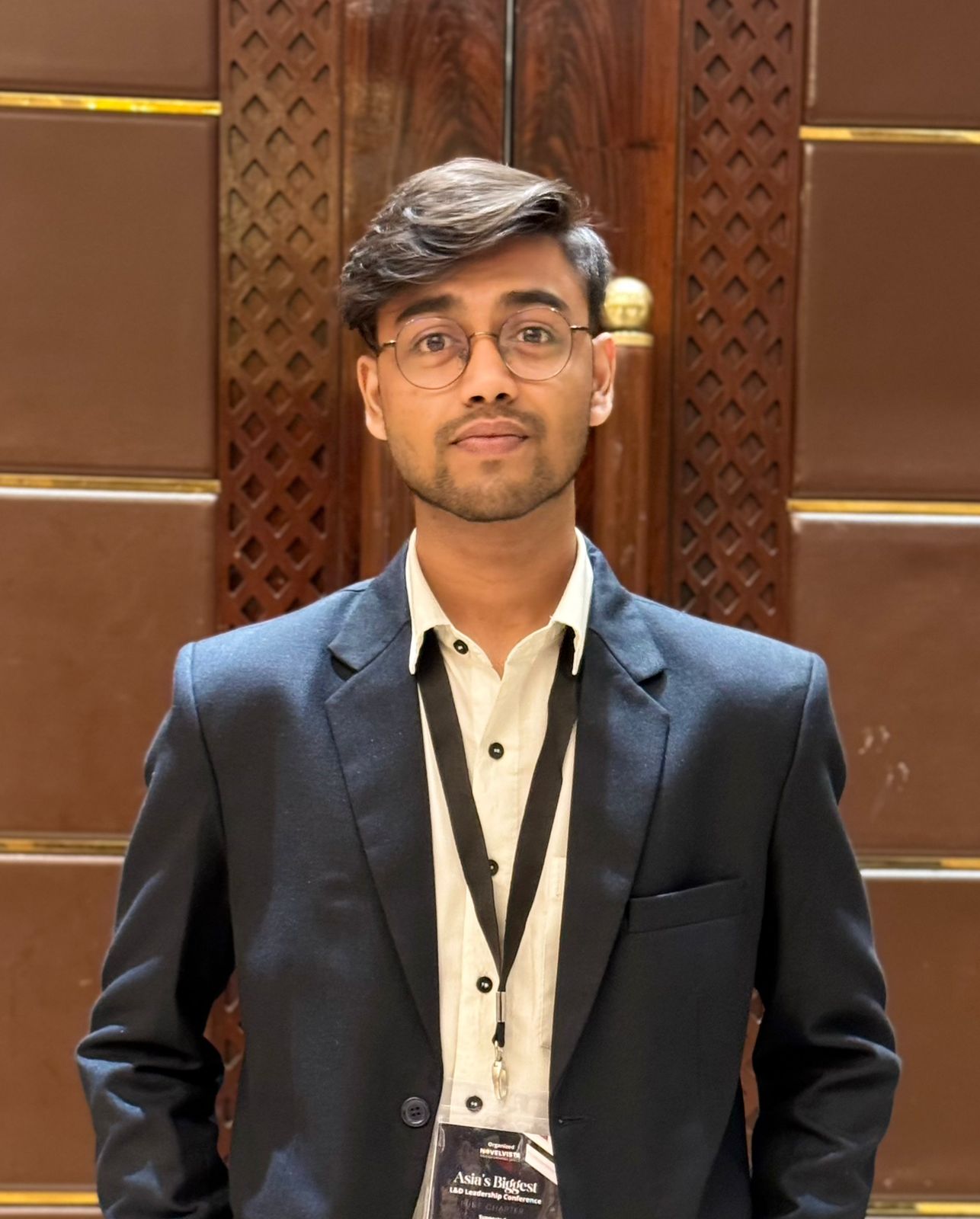
Akshad Modi
AI Architect
An AI Architect plays a crucial role in designing scalable AI solutions, integrating machine learning and advanced technologies to solve business challenges and drive innovation in digital transformation strategies.
Course Related To This blog
ISO 27001:2022 Lead Auditor
Confused About Certification?
Get Free Consultation Call