Job interviews can be stressful, even for experienced professionals. Those pre-interview jitters seem to intensify when you are aiming to advance your career by acquiring new skills such as Lean Six Sigma.
I still remember feeling anxious before my first Six Sigma interview after getting my Green Belt certification.
As a Six Sigma Yellow Belt or Six Sigma Green Belt certified candidate, I had no idea what kinds of questions they would ask about topics like process variability, DMAIC, or how to interpret capability metrics.
The good news is most Lean Six Sigma interviews focus on testing your grasp of the core methodologies and tools, regardless if you are Six Sigma Green Belt certified or Six Sigma Black Belt certified.
If you have a handle on the basic principles around things like Critical to Quality metrics, root cause analysis, Lean concepts, and statistical thinking, you’ll be fine!
To set you up for success and help you land the job, I’ve compiled this list of 20+ of the most common Lean Six Sigma interview questions along with expert answers.
They cover everything from defining central ideas like defects and process capability to Key tools like fishbone diagrams and FMEA.
Preparing answers to questions like these will equip you to demonstrate your understanding of Lean Six Sigma fundamentals during the interview, whether you’re an aspiring Green Belt or seasoned Black Belt. Now let’s get started!
Ace Your Lean Six Sigma Interview with These 20+ Questions
Q1. What is Six Sigma?
Answer:Six Sigma interview questions often focus on getting a basic understanding of the Six Sigma methodology.
As defined in Six Sigma interview questions pdf guides, Six Sigma is a complete set of tools and techniques for process improvement that focuses on enhancing quality by identifying and eliminating defects and reducing variability.
Interviewers want to know if you grasp the broad principles of Six Sigma, which are covered extensively in books and online resource materials for Six Sigma interviews.
Underpinning all certified Six Sigma methodologies like DMAIC or DMADV is a focus on customer needs, data-driven decisions, scientific and quantitative analysis and an orientation for continuous incremental improvement.
Q2. What are the different variations that are used in the Six Sigma process?
Answer:Several common Six Sigma interview questions aim to test knowledge of the key variations used in Six Sigma analysis.
As stated in many Six Sigma books and interview preparation materials, there are four vital metrics -Mean, Median, Range,andMode.
- Meanrefers to the mathematical average for given data sets related to a process whileMedianrepresents the midpoint if one were to arrange all observations in ascending or descending order.
- Rangeprovides the degree of dispersion between the highest and lowest figures.
- Modeindicates the value that occurs most frequently in the data set. Understanding variability in process performance is crucial for those implementing Six Sigma.
Interviewers want candidates to demonstrate fluency in discussing these fundamental Six Sigma metrics.
Q3. What is the difference between the Six Sigma DMAIC and DMADV methodologies?
Answer:One of the most frequent Lean Six Sigma interview questions focuses on distinguishing between the DMAIC and DMADV approaches.
DMAIC, which stands forDefine,Measure,Analyze,Improve, andControl, is an implementation framework aimed at incrementally upgrading existing processes that may be inefficient or prone to excessive defects.
As explained in Six Sigma interview articles and question-answer guides, it relies heavily on data garnered from the current process to identify root causes and improve overall performance.
DMADV is better suited for creating new processes, products, or services and has five phases -Define, Measure, Analyze, Design,andVerify.
While DMAIC assumes an existing process, DMADV requires extensive planning and rigorous testing for completely new solutions. Interviewers look for succinct and thoughtful responses that get to the heart of difference.
Q4. Explain the concept of the Fishbone diagram.
Answer:The Fishbone or Ishikawa diagram, often referred to as a cause-and-effect diagram, serves as a powerful visual tool for systematically identifying and categorizing potential causes of a problem.
This method is indispensable in Lean Six Sigma methodologies as it aids in drilling down to the root causes with precision.
By resembling the structure of a fish skeleton, this diagram encapsulates various factors that contribute to a specific issue. Employing categories like people, process, equipment, and environment, it facilitates a comprehensive analysis.
This intuitive approach enhances the team's ability to brainstorm and understand the intricate interplay of factors affecting a process or outcome.
Q5. What are the key principles of Lean Six Sigma?
Answer:The fundamental principles of Lean Six Sigma are crucial discussion points in any interview, emphasizing the candidate's grasp of process improvement strategies.
Prioritizing customer value is a cornerstone, showcasing a commitment to customer-centric approaches.
Additionally, the reliance on data-driven decision-making and the aim to reduce process variation underscores the candidate's analytical and problem-solving skills.
Interviewers often gauge a candidate's awareness of fostering a culture of continuous improvement, an essential principle showcasing adaptability and innovation.
Q6. What is the difference between load testing and performance testing?
Answer:In Lean Six Sigma interviews, discussing technical aspects such as load testing and performance testing demonstrates a candidate's familiarity with quality assurance.
Performance Testing, often explored in Six Sigma interview questions, assesses a system's responsiveness, while Load Testing scrutinizes its capacity under stress.
Both are essential in ensuring product reliability. These topics are likely to appear in Six Sigma interview questions and answers, with interviewers expecting candidates to articulate the nuances of each testing methodology.
Q7. What is the role of a Green Belt in Lean Six Sigma?
Answer:When discussing Lean Six Sigma interview questions, understanding the role of aGreen Beltis essential.
Trained in Lean Six Sigma methodologies, a Green Belt's responsibilities often include leading smaller process improvement projects, a topic frequently explored in Lean Six Sigma interview questions and answers.
Their contribution to data collection, analysis, and implementation aligns with the principles of Lean Six Sigma, making this a key area of discussion in Lean Six Sigma interviews.
Q8. What is a Top-down approach in the Six Sigma process?
Answer:The Top-down approach, a strategic aspect of Six Sigma implementation, connects organizational objectives with customer needs, making it a relevant topic in Six Sigma interview questions.
During interviews, candidates may be asked about their understanding of this approach, emphasizing its alignment with business strategy.
Despite its challenges, discussing how this method ensures process improvements directly influence customer satisfaction can showcase a candidate's depth of knowledge in Six Sigma.
Q9. Explain what you mean by FMEA.
Answer:FMEA, or Failure Modes and Effect Analysis, stands as a pivotal methodology in Lean Six Sigma interviews, often prompting insightful discussions.
This risk assessment tool evaluates the severity, occurrence, and detection of risks, allowing organizations to prioritize and address potential issues effectively.
Candidates may be asked to elaborate on how FMEA aids in proactive risk management, underscoring its significance in ensuring process robustness.
Q10. What are the three steps for Root cause analysis?
Answer:Root cause analysis is a critical aspect discussed in interviews, exploring a candidate's problem-solving skills.
The three steps involved serve as a structured approach for identifying and addressing the root causes of issues.
During interviews, candidates may emphasize the Open, Narrow, and Close steps, showcasing their ability to lead teams through problem-solving sessions.
Q11. What is the main difference between Lean and Six Sigma?
Answer:Understanding the distinction between Lean and Six Sigma is essential in Lean Six Sigma interviews.
This question explores a candidate's knowledge of both methodologies. Lean Six Sigma interview questions may specifically go into the seven steps of Lean, addressing aspects such as overproduction, waiting, transport, motion, over-processing, inventory, and defects.
Articulating these differences showcases a candidate's grasp of these methodologies, often a key focus in Lean Six Sigma interviews.
Q12. What is the significance of statistical analysis in Lean Six Sigma?
Answer:Statistical analysis holds immense significance in Lean Six Sigma, making this topic crucial.
Candidates are expected to articulate how statistical analysis provides valuable insights into process performance, identifies root causes of defects, and validates improvement efforts.
This may highlight the role of statistical analysis in making data-driven decisions and monitoring the impact of process changes.
Q13. What is the difference between Cpk and Ppk?
Answer:The distinction between Cpk and Ppk is a common point of discussion in Lean Six Sigma interviews, showcasing a candidate's proficiency in process capability indices.
Cpk, denoting the process capability index, evaluates how closely a process operates within its specification limits concerning the inherent variability.
Meanwhile, Ppk, representing the process performance index, assesses whether a sample generated from the process can meet Customer CTQs (Critical to Quality characteristics).
This nuanced understanding is crucial often going into statistical measures and their practical implications.
Q14. Name some Lean Six Sigma tools.
Answer:Candidates are often asked to showcase their knowledge of tools integral to the methodologies.
Key tools, such as Kaizen, Poka-yoke, FMEA (Failure Modes and Effect Analysis), and Value Stream Mapping, are critical discussion points.
Addressing these tools in Lean Six Sigma interview questions and answers highlights a candidate's familiarity with practical applications, reinforcing their capability to implement these tools in real-world scenarios.
Q15. What does DFSS stand for in the Six Sigma process?
Answer:DFSS, or Design For Six Sigma, is a key aspect, emphasizing a candidate's understanding of this business process management method.
DFSS extends traditional Six Sigma principles to various industries, including finance, marketing, basic engineering, process industries, waste management, and electronics.
Demonstrating knowledge of DFSS in Lean Six Sigma interview questions and answers underlines a candidate's awareness of methodologies applied throughout different business domains.
Q16. What is a data collection plan?
Answer:The concept of a data collection plan is often a focal point in Lean Six Sigma interviews, emphasizing a candidate's ability to gather essential information for process improvement.
The plan serves as a structured approach to collecting data from three primary sources: Input, focusing on data generation; Process, considering factors like efficiency, time requirements, cost, and defects; and Output, a direct measurement of efficiency.
Discussing the intricacies of a data collection plan showcases a candidate's practical approach to obtaining valuable insights.
Q17. Explain the difference between a Histogram and a Boxplot.
Answer:Distinguishing between a Histogram and a Boxplot is a common inquiry in Lean Six Sigma interviews, gauging a candidate's grasp of data visualization tools.
A Histogram depicts the frequency distribution of numeric data, while a Boxplot summarizes essential aspects of continuous data distribution.
This understanding is crucial in Lean Six Sigma interview questions and answers, reflecting a candidate's ability to choose and interpret appropriate graphical representations for data analysis.
Q18. What is VSM?
Answer:VSM, or Value Stream Mapping, is a central topic, emphasizing process optimization.
A candidate's familiarity with this methodology showcases their understanding of waste elimination and information flow mapping.
VSM serves as a valuable tool to enhance process efficiency by identifying areas for improvement and streamlining the delivery of products or services.
Q19. What is MSA?
Answer:MSA, or Measurement System Analysis, is a critical component discussed in interviews, assessing a candidate's awareness of measurement accuracy.
Candidates may elaborate on how MSA evaluates a system's accuracy, precision, and stability.
This topic in Lean Six Sigma interview questions and answers underscores the importance of ensuring reliable measurement systems for effective data-driven decision-making.
Q20. How to develop a SIPOC process map?
Answer:Developing a SIPOC process map is a fundamental skill that can showcase a candidate's ability to visualize and understand a process.
SIPOC, representing Suppliers, Input, Process, Output, and Customers, is a structured approach to summarizing a process's consecutive steps.
Candidates may discuss how this mapping helps in understanding current processes and proposing improvement suggestions.
50+ Six Sigma Interview Questions
Prepare for interviews at top companies:
IBM, Accenture, Infosys, TCS, Cognizant, Wipro,
and Capgemini.
Bonus Six Sigma Interview Questions and Answers for You
B1. How do you identify and prioritize improvement opportunities in Lean Six Sigma?
Answer:Identifying and prioritizing improvement opportunities in Lean Six Sigma involves a multifaceted approach.
One method is process mapping, which visually represents the steps in a process, helping to pinpoint inefficiencies and areas for enhancement.
Value stream analysis delves into the end-to-end flow of processes, aiming to eliminate waste and optimize efficiency. Customer feedback provides valuable insights into areas needing improvement from the end-user perspective.
Additionally,data analysis plays a crucial role, allowing for a quantitative assessment of process performance. Prioritization factors often include the impact on customers, potential cost savings, and alignment with strategic goals, ensuring a targeted and strategic improvement roadmap.
B2. How do you sustain improvements made through Lean Six Sigma?
Answer:Sustaining improvements in Lean Six Sigma is a continuous effort that involves the establishment of robust control measures.
This includes implementing standard operating procedures to institutionalize improved processes. Ongoing monitoring of key process indicators ensures that performance remains consistent.
Providing training to employees helps in embedding the new practices, and regular audits serve as checks to ensure adherence.
Engaging stakeholders throughout the process is vital, fostering a culture of continuous improvement and reinforcing the commitment to maintaining elevated performance standards.
B3. Can you explain the concept of the "Voice of the Customer" in Lean Six Sigma?
Answer:In Lean Six Sigma, the "Voice of the Customer" (VOC) is a cornerstone concept that emphasizes understanding and incorporating customer perspectives into process improvement initiatives.
The VOC represents the articulated and unarticulated needs, expectations, and requirements of the customer.
Capturing the VOC is instrumental in shaping project objectives, identifying critical-to-quality characteristics, and aligning process improvements with customer expectations.
Whether through surveys, direct feedback, or market research, integrating the VOC ensures that Lean Six Sigma efforts are customer-centric and geared towards delivering products or services that truly resonate with end-users.
B4. How do you handle resistance to change during Lean Six Sigma implementation?
Answer:Managing resistance to change is a pivotal aspect of successful Lean Six Sigma implementation.
Recognizing that resistance is a natural response to change, effective change management techniques become crucial.
Clear and transparent communication about the benefits of change helps in dispelling uncertainties. Involving stakeholders early in the process fosters a sense of ownership and reduces apprehension.
Providing training and support equips individuals with the skills needed for the new processes.
Visible leadership commitment demonstrated through active participation and support, reinforces the importance of the improvement efforts. By addressing resistance systematically, Lean Six Sigma initiatives can proceed with increased acceptance and collaboration.
Conclusion:
Preparing for Lean Six Sigma interviews doesn't have to be an intimidating experience, even though it may feel that way when facing the hiring manager.
Just remember that they simply want to understand your grasp of the key ideas and methods.
I hope reviewing these 20 sample questions and answers gives you greater confidence to show your stuff as a Green Belt or Black Belt.
If you're just starting on your Six Sigma journey, we recommend checking out ourSix Sigma certificationwhich can help you get a headstart on this path.
With the right preparation and certification to back up your knowledge, you'll be ready to knock your socks off and prove the value you can bring to continuous improvement efforts.
Best of luck landing the perfect job leveraging your Lean Six Sigma skills! Let me know how the interview goes.
Author Details
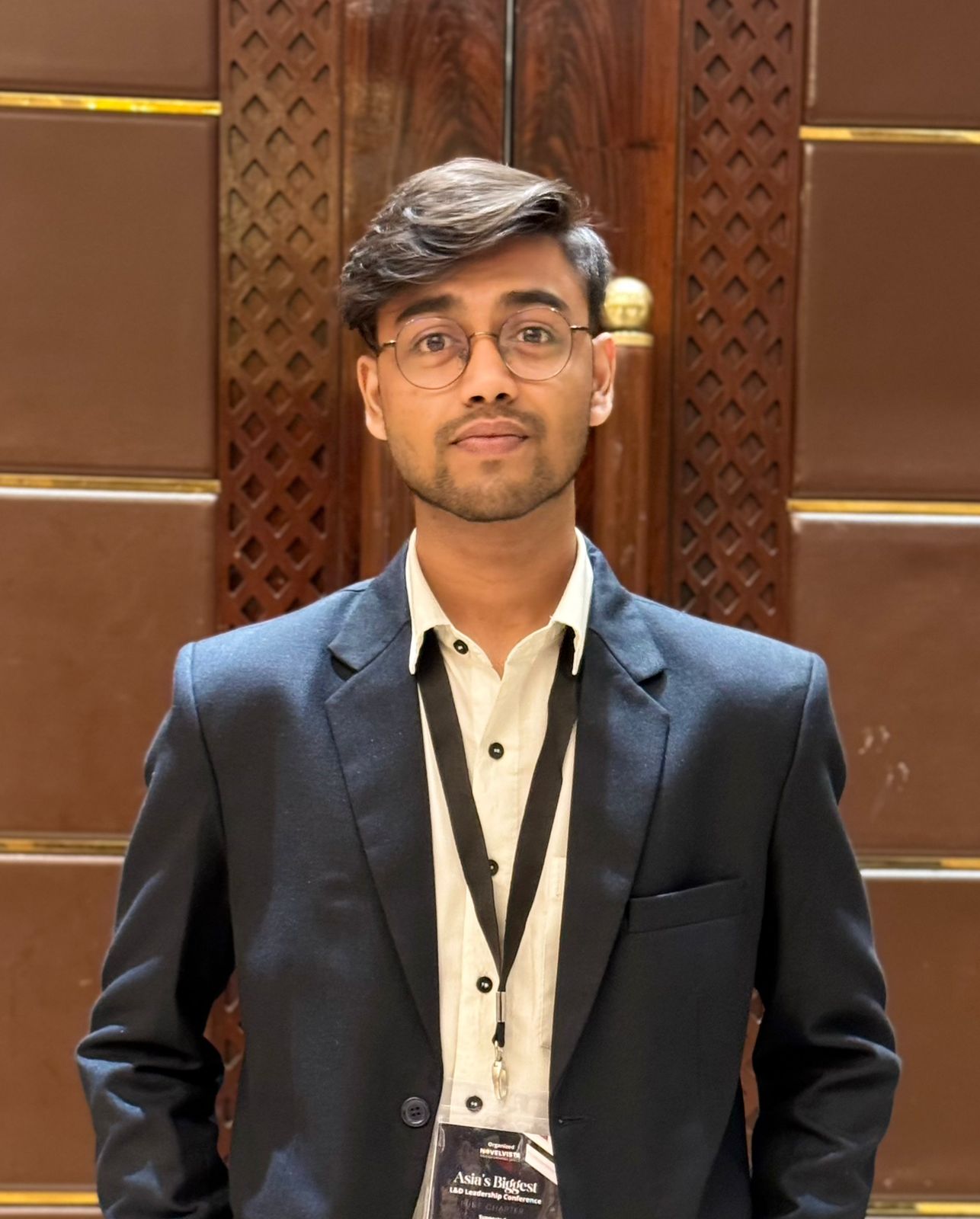
Akshad Modi
AI Architect
An AI Architect plays a crucial role in designing scalable AI solutions, integrating machine learning and advanced technologies to solve business challenges and drive innovation in digital transformation strategies.
Confused About Certification?
Get Free Consultation Call